The harmonized standard
EN ISO 12100:2010 – Safety of machinery – General principles for design – Risk assessment and risk reduction
constitutes a fundamental guide for all manufacturers who intend to CE mark their machinery according to the Machinery Directive 2006/42 / EC. It contains the basic principles for assessing the risk associated with a given machine and the guidelines for its reduction.
Chapter 6 is dedicated to this last fundamental aspect. The first paragraph highlights the levels to be taken to reduce risk:
- reduction of risks during design
- implementation of safety systems and / or complementary protection measures
- safety information for use
The order in which to undertake these actions must necessarily be that indicated above. The rationale behind this order invites manufacturers to take safety into account already in the design phase, where it is easier and above all more effective to make changes to the machine. All risks that cannot be reduced to acceptable levels simply by means of an intrinsically safe design must subsequently be mitigated by additional measures such as protections, guards and the like. Only as a last chance it is possible to use specific instructions and safety warnings reported in the machinery manuals.
The control system comes into play precisely in the second phase of risk reduction, especially in modern machinery which almost always integrates electromechanical and / or electronic components for their control. Where a function performed by a machine’s control system has direct repercussions on its safety, this function is called the “safety function”. Think, for example, of the classic red mushroom for emergency STOP. Or to a photoelectric barrier that stops the machine if an operator enters an unauthorized area.
The set of safety functions is called the “safety function list”. Each safety function must be appropriately characterized by a parameter that determines its efficiency in protecting against a risk of a given severity. For this purpose the standard has been prepared:
EN ISO 13849-1:2016 – Safety of machinery – Safety-related parts of control system – Part 1: General principles for design
In this standard, the characterization of each safety function is done by means of the parameter called “PLr”, short for “Required Performance Level”, indicating the minimum performance level that the safety function must reach in order to satisfactorily perform its action. The scale of possible performance levels is identified by lower-case letters of the alphabet, ranging from “a” to “e”, where “a” is the lowest possible level while “e” indicates the maximum achievable value.
For the determination of the PLr it is possible to follow the graph contained in Annex A of the standard.
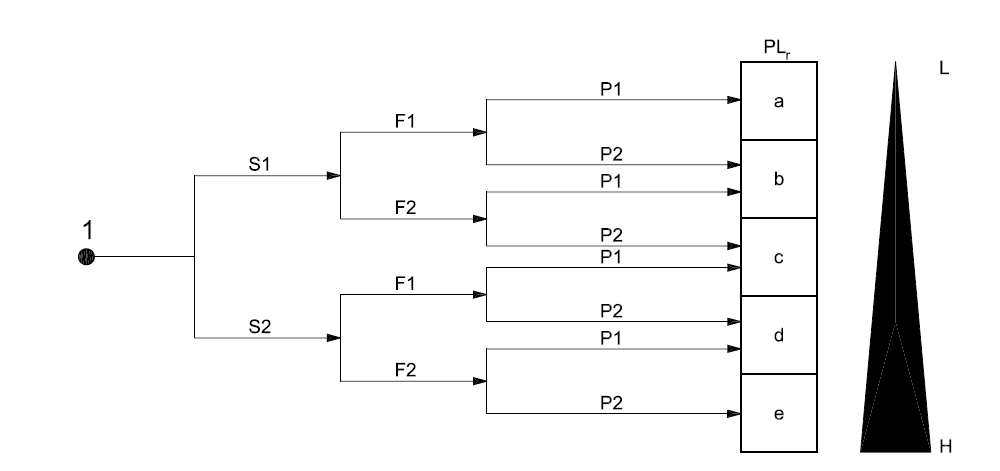
Starting from the point indicated with “1”, this graph must be traveled from left to right, making appropriate choices at each crossroads, corresponding to the choice of the following parameters:
- S: severity of injury
- S1: slight (normally reversible injury)
- S2: serious (normally irreversible injury or death)
- F: frequency and/or exposure to hazard
- F1: seldom–to-less–often and/or exposure time is short
- F2: frequent-to-continuous and/or exposure time is long
- P: possibility of avoiding hazard or limiting harm
- P1: possible under specific conditions
- P2: scarcely possible
Going through the graph in the figure and choosing the parameters S, F and P according to the specific cases, you reach one of the boxes corresponding to the PLr – required performance level.
The next step is to verify that the PL reached by the safety function is equal to or greater than the PLr. For this verification, the rule must be followed
EN ISO 13849-2:2013 – Safety of machinery – Safety-related parts of control system – Part 2: Validation